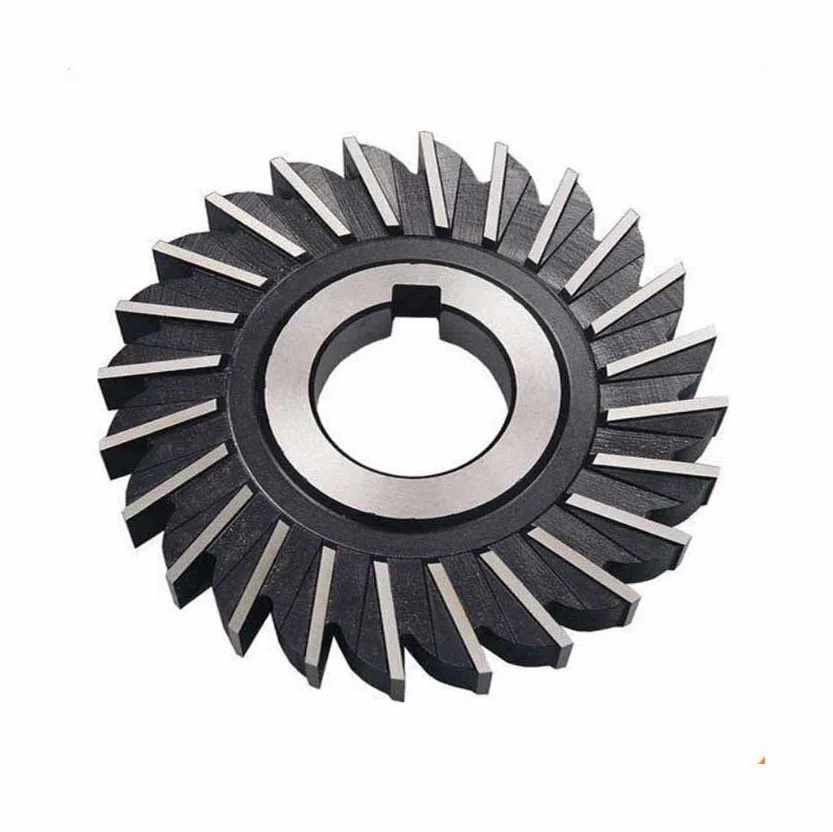
Precision machining is necessary in numerous enterprises. It is particularly important in aerospace and automotive, where exactness and quality are noteworthy. Among many methods, one critical one is side milling. The side milling cutters are used to remove material from the flank of the workpiece. This is utilized to get accuracy. Today, we will explore significant strategies for using these cutters properly in precision machining.
What is Side Milling?
It is a unique procedure in which spinning blades remove material from the sides of a workpiece to improve its appearance and functionality. It differs from end milling, where the cutting is done at the tip of the edges. It uses the cutting borders along the side of the instrument. This is used for creating flat surfaces, grooves, and detailed profiles. Side milling cutters usually have teeth along the outer border, which helps remove the material when it comes into contact with the piece.
Choosing the Right Side Milling Cutter
The first step in this operation is to select the proper cutter. These factors should be considered:
Material: Get cutters made with materials like carbide HSS. According to the workpiece, choose which one to use. They are generally used for Hard Metals, whereas HSS cutters are better suited for softer materials.
Cutter Size: It should be set according to the dimensions of the piece you are working with. Suppose the workpiece is big and uses a larger cutter. For detailing and fine additions, use a smaller blade.
Tooth Geometry: The number and shape of teeth affect cutting performance. An increased number of teeth can offer a smoother finish but can also build up heat. Fewer allow for faster material removal.
Techniques for Side Milling
Take a look at these factors:
Machine Setup: Your machine must be all set. The blade should align with the workpiece. The material surface should face the cutter. If the setting is not done properly, it might result in faulty results.
Tool Maintenance: Proper upkeep is essential to extend the tool's life. Insect for wear and tear and address potential issues before it terminates and breaks the cutter. Replacing or sharpening tools when needed ensures consistent cutting performance. Moreover, keeping the machine's surroundings neat from debris can save both the blade and the workpiece.
Surface Finish and Accuracy: Another major benefit of side milling is achieving high-quality surface finishes and specific tolerances. Multiple lighter cuts can be made as the finishing passes, reducing the need for additional post-machining work.
Conclusion
Side milling cutters are essential for achieving the perfect smooth look on various surfaces. By following the abovementioned factors, you can learn how to choose a proper cutter and strategies to maintain and use it properly. It is used in various domains that require quality and performance.
Maxwell Tools is a popular name in the industry. They are appreciated for their products and exceptional customer service. You can find anything from work rolls, metal slitting saws, separator discs, metal spacers, and rubber-bonded.
Write a comment ...